As kids don their scariest Halloween costumes and run all over the neighborhood collecting Hershey’s Bars, Reese’s Peanut Butter Cups, Kit Kats, and Skittles (and parents add a toothbrush to the shopping list), a feeling of nostalgia has taken over.
As a kid, my siblings and I would always dress up (though usually not in super scary costumes), and join the other neighborhood kids for trick-or-treating under the supervision of neighborhood dads. Though I use “supervision” here loosely! The moms stayed home to pass out candy and prepare the traditional Halloween dinner of homemade pizza (or frozen pizza, or delivery pizza).
The local Property Owner’s Association was known for the haunted house they created in the banquet room of their building. So, every year, we’d all take a walk through that and have the bejesus scared out of us.
At the end of the night, we’d dump our candy bags, separate candy by type and make our trades. We’d also have to pay dad’s trick-or-treat charge - Heath bars.
Last year was my and my son’s first Halloween in our new home and I passed out WAY more candy than anticipated. We had to break into the pantry and pass out fruit snacks, Goldfish crackers and Little Hug Fruit Barrels and STILL had to turn off our light with an hour left of trick-or-treating. This year, I’ll be way more prepared.
Speaking of preparation, Mid-States Concrete Industries has 77 years of experience working with our clients to ensure projects come in on-time, on-budget, and on-target. Each project offers its own unique goals and opportunities. We partner with our customers to find the right solutions for your projects.. With dedicated sales, estimating, project management, engineering, design, production, and construction teams, Mid-States has all the experts in place to meet your precast needs.
Our team will ask questions and listen to your objectives and goals so we can apply the latest techniques to your projects, while adhering to the strictest safety standards in the industry. There’s nothing scary about that!
Precast concrete offers aesthetic versatility, structural versatility, and use versatility. Precast concrete is efficient, as it offers site efficiency, energy and operations efficiency, and risk reduction. Precast concrete is resilient. It offers structural durability, multi-hazard protection, and life safety and health benefits.
To learn more about how precast concrete can benefit your next project, call us at 800.236.1072 or email us at sales@msprecast.com.
Precast Chalk Talk: Episode 49
In this episode of Precast Chalk Talk, President Hagen Harker talks with members of our Installation Team about how they install our precast concrete components.
Watch now >>
Questions? Comments? Ideas for a future episode? Email chalktalk@msprecast.com.
Find every episode of Precast Chalk Talk >>
Find additional square footage with precast
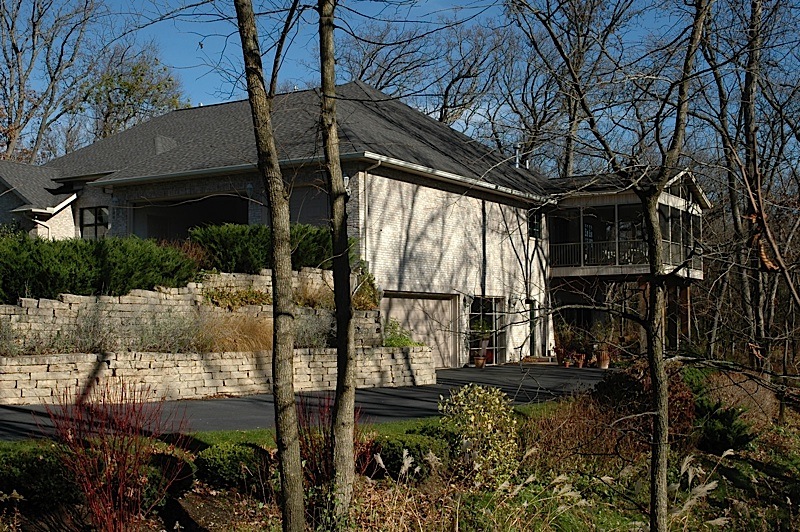
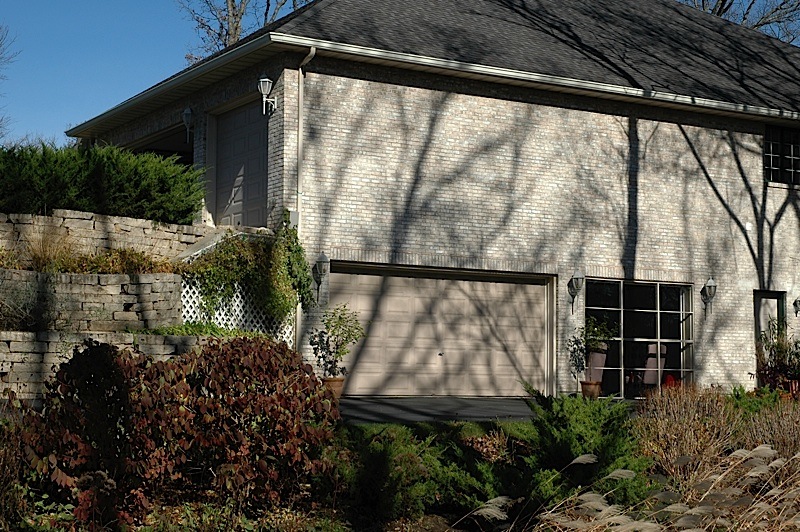

Hollowcore is the most versatile of all Mid-States Concrete products as it can be sized and shaped to meet virtually any need, offering true design flexibility.
When it comes to home construction, hollowcore offers flexible options for making the most of a space and creating the room – or entire home – of dreams. Nearly all single family home jobs that come through Mid-States Concrete feature hollowcore only and most are for new construction. Projects are generally for garages with usable space below. The space is used for everything from theaters to home gyms to sports courts, golf simulator rooms, and storage. We have also helped customers create spaces for a wine cellar under their front porch, and small areas as safe rooms.
One Meadow Road Estates home utilized about 900-square-feet of hollowcore to construct a workshop below their garage. The plank allowed for 28-feet of clear wall-to-wall space, with no columns disrupting the floor flow. The precast ceiling also allows for vehicle parking above.
Among the many benefits precast provides customers include: noise reduction and no squeaky floors; insurance benefits due to the two-hour fire rating; long spans from wall-to-wall, eliminating steel beams and columns in the basement; and even the ability to install in floor heating in the poured topping.
In order for Mid-States Concrete to provide an accurate quote for a home project, we’ll need a drawing with dimensions, or to be provided the dimensions by phone. It is also important for the contractor on the project to determine if they want our crews to install the precast, or if they plan to install it themselves. Roughly 70% of customers choose to have Mid-States install for their home project. If Mid-States crews are installing the project, a Project Manager will be sent out to field measure and verify conditions – such as placement of power lines, trees, and site access. If Mid-States is not installing the project, field measuring is the responsibility of the customer.
Regardless of who installs the project, the customer will always see shop drawings for their approval prior to manufacture of their pieces. Precast is typically ready for install four- to eight-weeks from signing the contract.
Interested in learning more about how to utilize precast on your next home project? Contact Ian Lewellin at 800.236.1072.
Achieving your aesthetic vision with precast concrete finishes
Hempstead High School: Dubuque, IA
When it comes to finishes for precast concrete wall panels, the possibilities are (nearly) endless.
Precast wall panels offer a large variety of finishes and applications to choose from. When it comes to selecting an architectural finish and making sure the aesthetic you are shooting for is the aesthetic you get, it is important to keep a few things in mind.
Having the finishes of the panels spelled out and noted in the specifications and also on the building exterior elevations will help the precast manufacturer in pricing.
Most buildings in our area will be in the limestone color range due to the Midwest having a lot of limestone quarries.
Certain finishes with special aggregates/sands can get costly depending on the distance the materials need to be sourced from.
Bump outs on the exterior face can cost more due to material costs.
If using thin brick, the exterior wythe needs to be a minimum of 4” thick.
While acid etching the panels on the front face, you can get acid that will run down the backside which is the interior face of the wall. If a good quality paint is used on the interior, this will most likely not be an issue.
Staining and/or painting are typically done by the painter on the project after panels are installed.
Interior finishes are typically a float finish or a steel trowel.
Wall panels are a popular structural and architectural system in commercial, industrial, education, multi-family, medical, municipal, and other markets. They can be designed as non-loadbearing or loadbearing, carrying floor and roof loads, as well as lateral loads. Panels may be solid, composite, non-composite or composite with continuous insulation.
Our standard finishes include light acid wash, light sandblast, medium sandblast, heavy sandblast, light water wash, medium water wash, and heavy water wash. While some of our most popular finishes include a light sandblast finish with a buff color and a plain grey steel form finish that will be painted, we also offer a variety of unique finishes including thin brick, graphic concrete, and finishes using form liners for patterns like stone, wood, ribbed and split-faced block.
One thing to keep in mind is that we want to deliver what an architect is expecting. That means, if the new panels are to match an existing building, we will travel to the existing building, determine the finish, and provide a sample that can be used for pricing and production. The architect will typically use these samples to put them in the specification during the bidding process.
Additionally, for all wall panel projects, we will go through the process of a sample approval prior to production. The sample piece will incorporate details like reveals, insulation, corner finish, color of the mix design and texture.
Mid-States Concrete is a PCI-certified architectural precast concrete producer. We will provide a uniform, high quality building façade to meet your aesthetic needs.
Precast Concrete Provides Quick, Aesthetically Appealing Podium for Building
When the luxury apartments known as Parkview Lofts started the construction process for Parkview II, the construction team knew precast was the way to go for the building’s podium.
A common podium configuration consists of one or more levels of a hollowcore, beam, and column parking structure below ground with the upper deck, often hollowcore, providing both fire separation and structural transfer. In addition to the parking structure below, podium configurations often include an additional story of precast at the ground level for mixed use space, with four or five stories of wood-framed construction above.
“We have kind of a podium construction there for floors of wood frame above the precast and we needed a three-hour fire rating,” said Shane Morelock, Project Manager with Hodge Construction, the general contractor on the project. “Precast is really the most economical to reach that and not have to do additional fireproofing, and structurally it works.”
The project also utilized precast concrete walls for the building’s elevator shaft and stair shafts. The elevator walls were full height and the stair shaft walls were up to the podium. Morelock acknowledged the benefits of using precast for this, noting that when using precast, haunches are built in and coordinated. This saves time as an additional subcontractor is not needed on site then. The elevator embeds were also cast into the panels, getting that task done ahead of time as well.
Mid-States Concrete Industries provided nearly 15,000-square-feet of hollowcore, 21 beams, 15 columns, and more than 3,000-square-feet of wall panels for this project.
While Hodge Construction considered masonry for the elevator shaft, precast ultimately made more sense. In addition to the speed of erection for this project, other benefits included the elimination of fireproofing, which would have been necessary if they had used structural steel.
“Just the erection speed of it would be the biggest [benefit],” Morelock said. “This one was just shy of two weeks for erection.”
Morelock also praised the preconstruction work on the project, acknowledging the upfront work helped to eliminate some columns, which opened up the garage a bit, providing more useful space and saving money. He also said the shop drawings process went well with the 3D drawings helping to visualize how all the components work together and where embeds and things were needed. Morelock added that installation went smoothly and everyone on site was easy to work with and he was pleased with the quality of the precast components.
“I think this one went about as smooth as you could hope for,” Morelock said.